The plastic extrusion process does exactly what it says on the tin – extruding plastic to create both standard and bespoke profiles. In fact, we can outline the steps as simply as follows:
- Granular plastic is held in a hopper
- It is moved through the heating chamber
- Once the polymer has been melted, it is pushed through a die, which will form the shape of the extrusion as required by the specifications
The plastic extrusion process takes granular pieces of plastic through various components of the extruder to end up in a continuous profile with the help of heat and pressure.
Although plastic extrusion has a lot of elements and phases, it is quite a simple process that leads to the development of specific components. More pieces can be processed accurately and in a time-efficient manner thanks to plastic extrusion.
While the steps of the process itself sound quite simple, as you can imagine it is the machinery itself that undertakes most of the technical side of things. Plastic extrusion machines are complex, with systems in place to create the desired profiles down to the tiniest specified detail. These, along with the expert supervision of our extrusion team here at Rocal Extrusions, ensure you get the profiles you need.
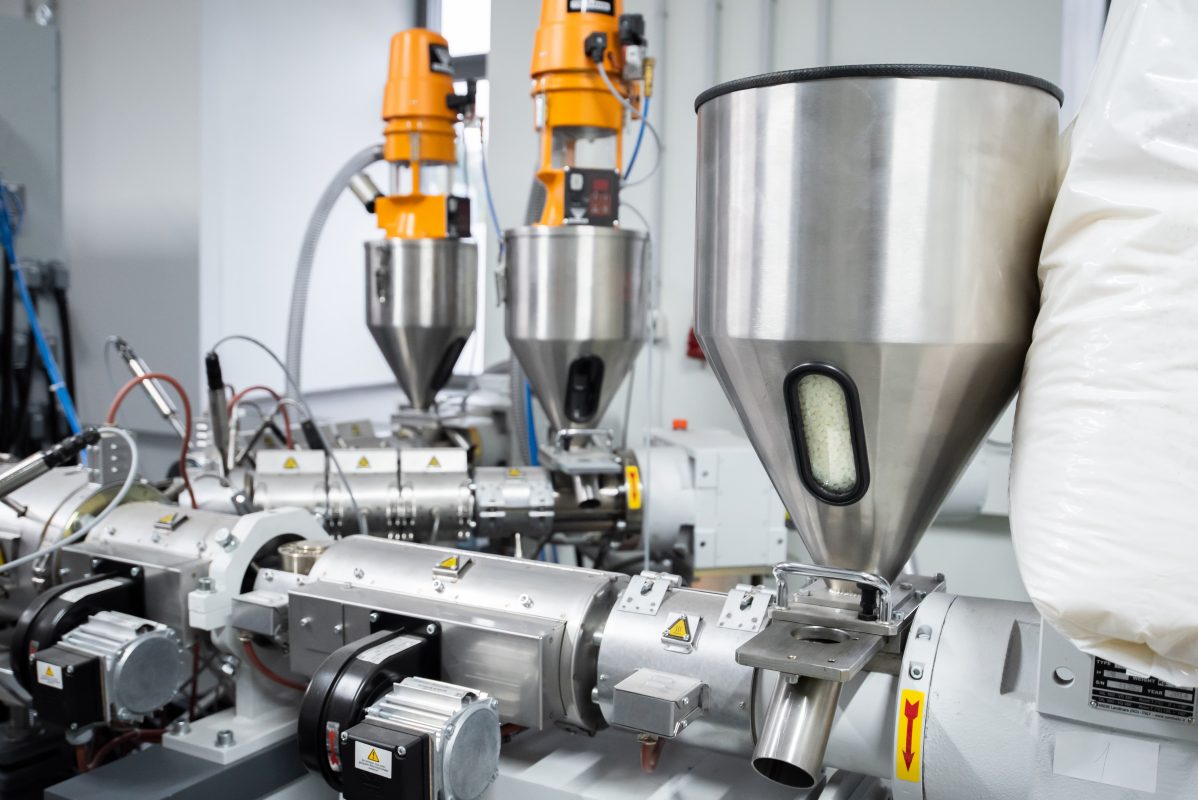
Advantages of Plastic Extrusions
Plastic extrusion is one of the most used and highly regarded processes in the plastic industry due to its many advantages. We could wax lyrical about the benefits of our products and machinery, but for now, we’ll outline a few of our team’s favourite positives.
- Minimal waste production – thermoplasics used in extrusion can handle multiple processes, so any would-be waste can simply be reshaped and reused
- Complex cross-sections – the bespoke manufacturing process means your required specifications can be achieved through innovative, intelligent production
- Continuous operation capabilities – thanks to ongoing processes, we’re able to pass on to our customers lower costs and faster turnaround times
- Versatility of materials – extrusion processes can work with many types of raw materials, including both flexible and rigid plastics as the job requires
- High-quality surface finish – exceptional results to give the aesthetics you need, as well as the performance beneath the surface that you can rely on
- Customisability – bespoke options available to suit your spec, such as fire resistance, improved durability and environmental sustainability
The advantages of plastic extrusions are many, as are the advantages of working with an experienced, reliable company such as Rocal Extrusions. With many years of experience under our belts and many more ahead, you can enjoy all these benefits and more for your next project.
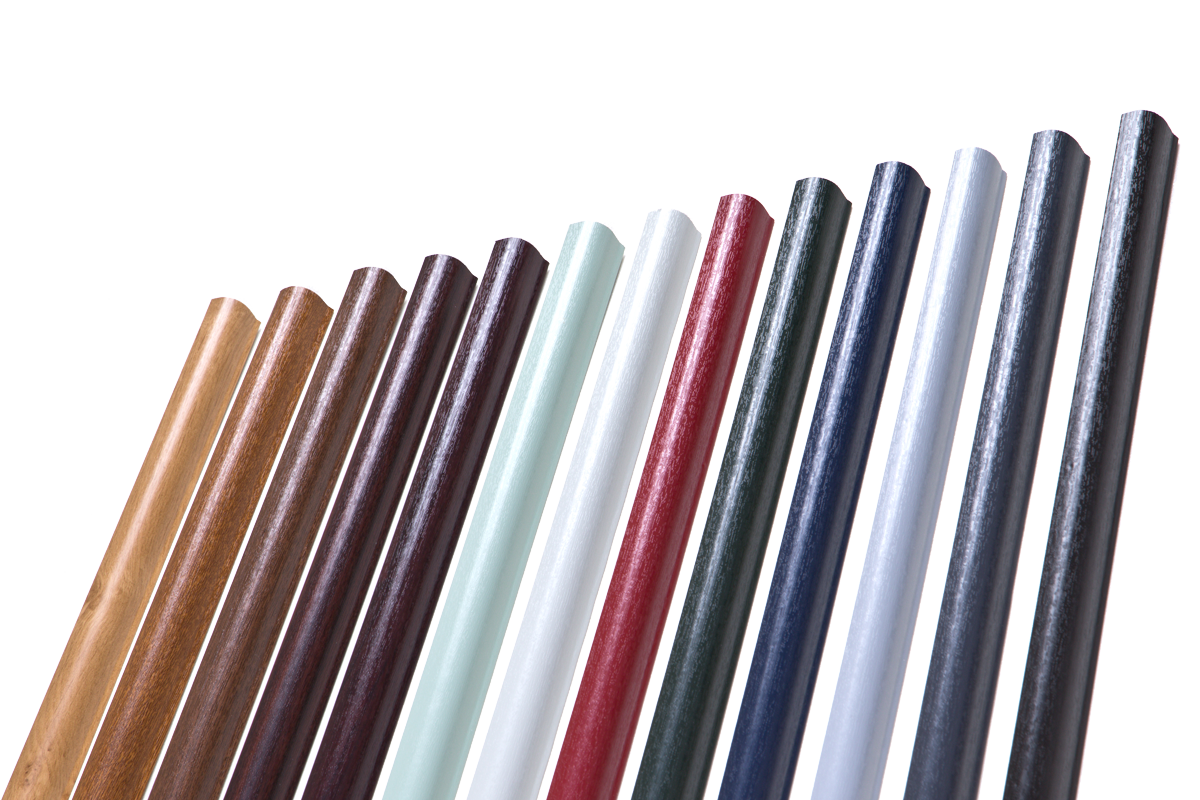
Standard and Bespoke Extrusions
Whether you’re looking for off-the-shelf standard profiles or something a little more bespoke, you can rely on the team here at Rocal Extrusions. Now you understand a little more about what plastic extrusion is, how the process works and the advantages it offers, we hope you can also see why choosing the right company to partner with is key.
We’re proud to offer bespoke tooling to create components that will suit your specifications. Our experienced toolmakers are on-hand to not only create the profiles you need, but also offer expert advice that can make all the difference. Alongside standard profiles, we can provide co-extruded, flexible and rigid profiles – all of which you can find out more about by exploring our website.
When you’re ready, or for more tailored advice for your project, we welcome you to get in touch with our extrusions team on 01652 225 200 or via our online contact form. We’ll be happy to help and tell you all about how our plastic extrusion processes will work for you.