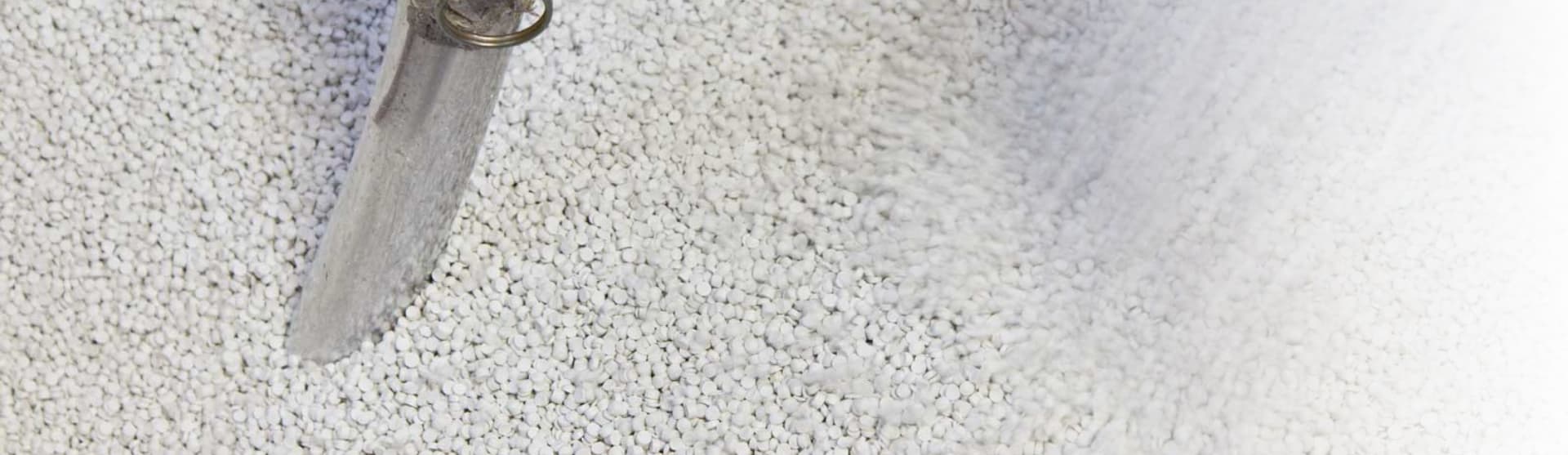
Materials Selection.
Polymer Materials for Extrusion
Our expert technical design team have been specifying unique polymer blends to produce plastic extrusions with individual properties for over a decade. Our knowledgeable team can advise on the right materials for your desired application and setting.
Below, you can gain an understanding of the materials we extrude and their properties.
Rigid Plastic Extrusion Materials
With over a decade of experience in plastic extrusion we have developed an extensive portfolio of rigid profile tools. Our Rigid plastic extrusions are used in various industries, including construction, automotive, and fenestration, for applications such as window and door frames, pipes, tubing, and decorative mouldings. These extrusions offer durability, dimensional stability, and resistance to impact and corrosion, making them suitable for a wide range of structural and functional purposes.
Acrylonitrile Butadiene Styrene (ABS).
Acrylonitrile Butadiene Styrene (ABS) is an ideal material wherever superlative surface quality, colorfastness and luster are required. ABS is a two phase polymer blend. A continuous phase of styrene-acrylonitrile copolymer (SAN) gives the materials rigidity, hardness and heat resistance. The toughness of ABS is the result of submicroscopically fine polybutadiene rubber particles uniformly distributed in the SAN matrix.
- High impact strength and resistant to abrasion
- Performs well in both high and low temperatures
- Good chemical resistance
- Fire resistance grades available
- Strong adhesive properties
- Medium Cost
- Automotive parts
- PPE
- Construction Materials
- Medical Devices
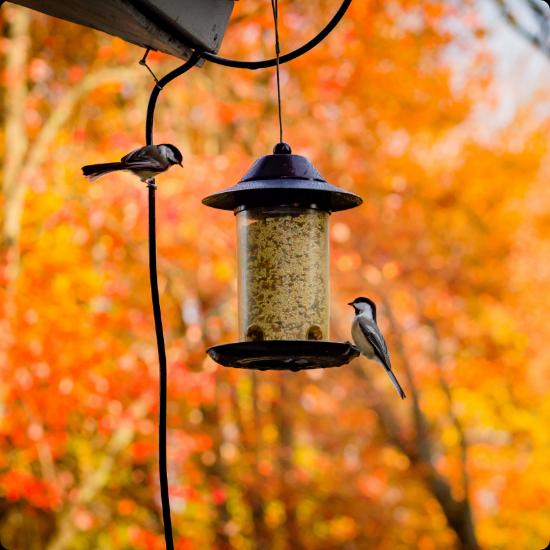
Unplasticised Polyvinyl Chloride (UPVC).
UPVC is a type of rigid plastic commonly used in the construction industry for doors, windows, piping, and other building materials. Unlike traditional PVC, which contains plasticisers to make it more flexible, uPVC is rigid and does not contain these additives. It’s characteristics make uPVC a preferred choice for windows and doors in residential and commercial buildings, as well as for plumbing and drainage systems.
- Lightweight but strong and resistant to mechanical stresses
- Highly durable and resistant to degradation from sunlight, weathering, and chemical exposure.
- Resistant to moisture, humidity, and temperature fluctuations.
- Good chemical and fire resistance
- Recyclable and can be repurposed into new products
- Window and Door frames
- Pipes and tubing
- Roofing and Cladding
- Conservatories
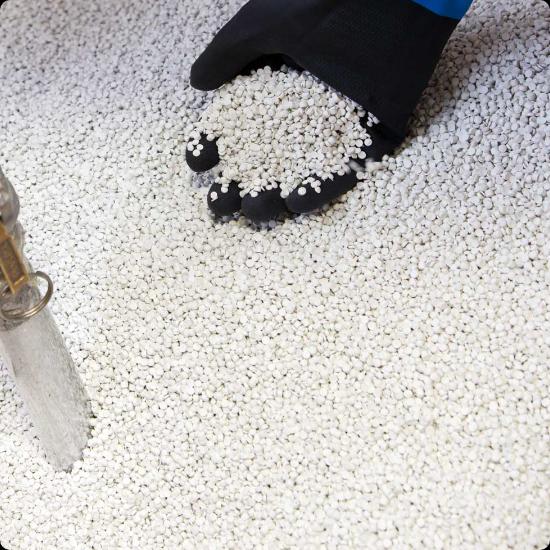
Polypropylene (PP).
Polypropylene is a versatile thermoplastic polymer resin widely utilised in various industries for its exceptional properties. Polypropylene is one of the most commonly used thermoplastics in the world, used in a variety of industrial and domestic applications. PP is suited to the manufacture of both flexible and rigid extrusions.
- Excellent strength to weight ratio
- Easily coloured with pigments
- High melting point
- High chemical and moisture resistance
- Resistant to UV damage
- Packaging and Containers
- Parts and Components
- Medical Appliances
- Window & Door seals and trims
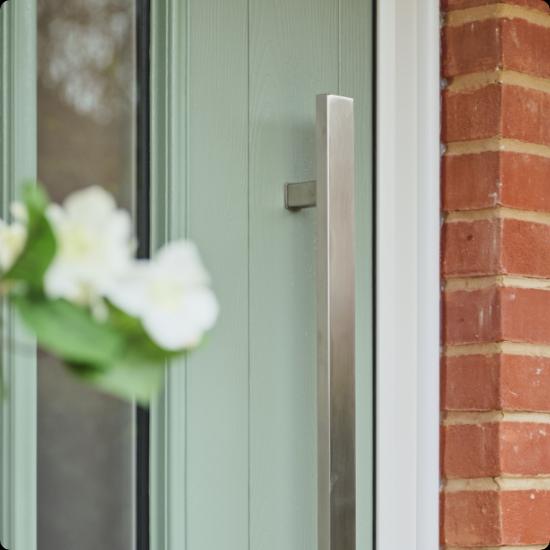
Blown PVC.
Blown PVC is also known as Cellular PVC. This polyvinyl chloride type has lots of tiny bubbles inside the material structure. It offers the strength and versatility of traditional PVC while providing enhanced insulation properties and reduced weight. Blown PVC is commonly used in construction for applications such as trim boards, mouldings, decking, and siding, offering durability, low maintenance, and resistance to moisture, rot, and insects.
For more information on our Blown PVC products, explore our TimbPlas product.
- Lightweight but strong and resistant to mechanical stresses
- Highly flame retardant
- Timber-like characteristics but with minimal maintenance requirements.
- Resistant to warping, splitting and bowing.
- Recyclable and can be rechipped.
- Good bonding
- Easily moulded
- Timber alternative products
- Construction
- Window and Door surrounds
- Structural framework
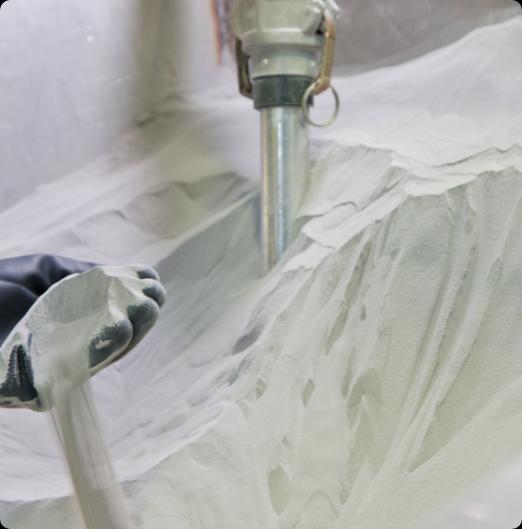
Flexible Plastic Extrusion Materials
Flexible plastic extrusions are used in a wide variety of different applications. Depending on the polymer mix used, Rocal Extrusions can produce flexible profiles that possess varying levels of rigidity to suit your desired use. Unlike rigid profiles, flexible plastic extrusions can be manufactured with irregular wall thicknesses, making them ideal for use in sealing systems or connecting components.
Low-density polyethylene (LDPE).
Low-Density Polyethylene (LDPE) is a highly versatile thermoplastic polymer known for its wide range of applications across a variety of industries. It is formed through the polymerisation of ethylene monomers and is characterised by its low density. LDPE offers a unique combination of properties that make it suitable for a diverse range of applications and a popular choice for bespoke extrusions.
- Highly flexible with good elasticity
- Impact and puncture resistance
- Good chemical and moisture resistance
- Naturally transparent - easily pigmented
- Easily processed in a variety of manufacturing methods
- Recyclable
- Packaging
- Tubing
- Appliance components
- Office equipment
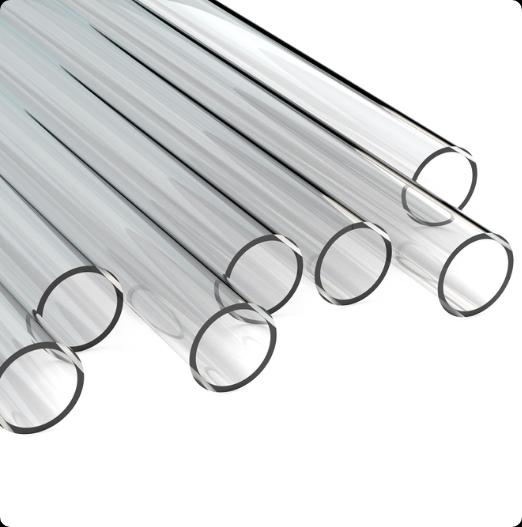
High-density polyethylene (HDPE).
High-Density Polyethylene (HDPE) is a versatile thermoplastic polymer recognised for its various applications across a range of industries. In a similar way to LDPE, high-density polyethylene is formed through the polymerisation of ethylene monomers and is characterised by its high material density. HDPE offers a range of properties that contribute to its versatility and suitability for diverse applications.
- High strength to weight ratio
- High impact strength and damage resistance
- Chemical and Solvent resistance
- Low moisture resistance - suitable for external uses
- Recyclable and can be repurposed into new products
- Easily pigmented
- Bottles and Packaging
- Pipes and tubing
- Medical Devices
- Automotive Parts
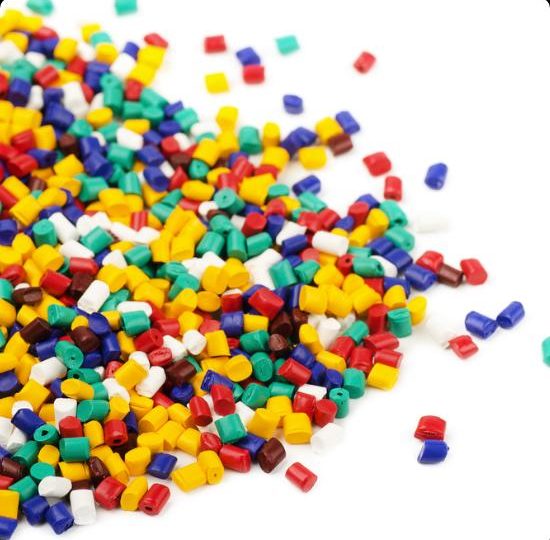
Polyvinyl Chloride (PVC).
PVC is widely adopted thermoplastic polymer that has widespread industrial applications. Polyvinyl chloride (PVC) is distinct from uPVC (Unplasticised Polyvinyl Chloride) primarily in its composition and properties. While both are derived from vinyl chloride monomers, uPVC differs in that it does not contain plasticisers, which gives it enhanced rigidity and durability compared to PVC. uPVC is commonly used for applications requiring high strength and resistance to weathering, whereas PVC, with its greater flexibility and versatility, suits broader applications.
- Varying levels of flexibility
- Flame retardant
- Good chemical and biological resistance
- Easily pigmented
- Easily processed in a variety of manufacturing methods
- Low Cost
- Window and Door frames
- Polyvinyl Chloride (PVC).
- Seals and Gaskets
- Office equipment
- Tubing
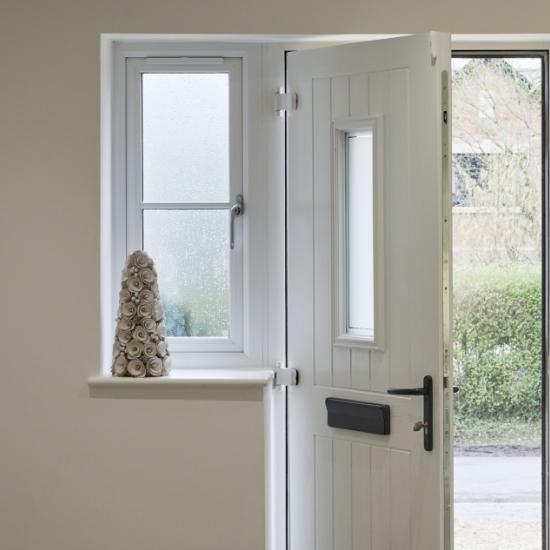
Get A Quote.
Fill in as much information on the form, press
submit and we will get back to you with a quote.